Reciprocating Compressor Applications
Reciprocating compressors are unique pieces of equipment as they contain active components that are moving in rotary as well as linear directions. They also play a vital role in any process that they are employed in. Therefore, a reciprocating compressor’s health must be monitored doing more than just following the usual vibration monitoring rules.
Reciprocating compressors are positive displacement machines used to compress air or other gases through the action of a piston or pistons moving in a back-and-forth motion called strokes. Reciprocating compressors can also be vertically mounted, whereas the piston motion is up and down. As the piston moves within the cylinder, suction valves open and the piston action creates a vacuum, drawing gases into the cylinder, and then the piston compresses the gas within the cylinder. As the gas is compressed, the discharge valve opens, allowing the pressurized gas into the discharge chamber. The discharge chamber releases the compressed gas into the process or pipeline. In other words, the piston moves reciprocally to compress the gas. These types of compressors are considered the most energy-efficient for most applications. Because there are many different reciprocating compressors, they can be found across various industries. The different types of compressors are:
- Single Acting
- Double Acting
- Diaphragm Type
- Single Stage
- Two Stage
- Multi-Stage
The majority of applications for reciprocating compressors are in the oil and gas industries. Oil refineries use these compressors for processes that require high pressure delivery of essential gases. The natural gas industry also utilizes reciprocating compressors to transport gas via cross country pipelines. These compressors can also be found in chemical plants, refrigeration plants, or air compressors for tooling. They even have a place in agriculture, HVAC systems, automotive workshops, and dental offices.
Regardless of the industry, reciprocating compressors are typically considered critical for the facility and expensive to acquire. Protecting this equipment should be a concern for any business that operates these important machines. Metrix provides a cost-effective monitoring solution that will help you get the full value from your reciprocating compressor.
Vibration Monitoring of Reciprocating Compressors:
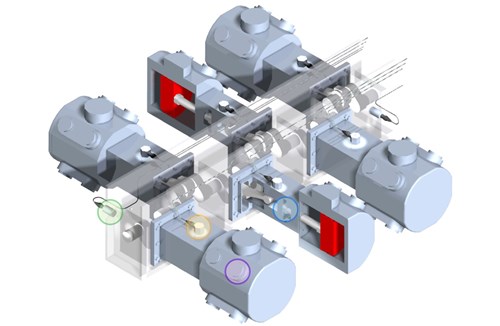
Rod Drop / Rod Position Digital Proximity System > MX2034
Impact / Crosshead Acceleration Impact Transmitter > IT6810, IT6811, IT6812
Crankcase Velocity Seismic Transmitter > ST5484E
Temperature Monitoring > DATAWATCH IX
Click the chart to view Recip Failure Modes
See our Recip Monitoring Animation
Why choose Metrix for monitoring your reciprocating compressors?
The answer is simple: better value.
1. Scalability
Metrix is the only provider to offer monitoring solutions easily scalable to the various sizes of reciprocating compressors, namely packaged/skid-mounted up to API 618 machines. In contrast to their much larger API 618 counterparts, packaged recips are typically smaller in size, but can still occupy a prominent role in the plant. While a complex measurement suite and accompanying diagnostic software may not be appropriate, Metrix provides affordable and comprehensive solutions for this smaller – but no less important – class of machines.
Metrix is now able to offer a focused solution for API 618 type recips including shutdown and alarm for frame vibration, impact severity, rod drop, and crosshead acceleration. Large or small, Metrix truly delivers a scalable solution.
2. Simplicity
Our approach to reciprocating compressor monitoring is to simplify it without sacrificing effectiveness. Accordingly, we have designed our offerings to use simple measurement concepts focused on the four key areas in which reciprocating compressors are most prone to mechanical problems. Metrix is the only company offering 4-20mA transmitter-based solutions. Our solutions focus on simplifying the user experience for installing, maintaining, and using the instrumentation, while delivering outstanding results and excellent value for the money.
3. Experience
Metrix monitors an estimated 3,800 reciprocating compressors around the world – more than any other provider. Our solutions have been proven in use for more than two decades and are purchased by OEMs and end-users alike. We also maintain open communication with our customers, ensuring reliable feedback and subsequent improvement for our products. The 5580 and SW5580 products are good examples of that feedback.
4. Innovation
More than twenty years, Metrix became a leader in the industry and has remained as such with our patented impact measurement technology. We developed this technology because we recognized hard workers like you needed a reliable yet simple way to detect problems in your reciprocating machines, such as looseness in crosshead shoes, wrist pins, connecting rods/nuts, and other components. We also pioneered the first commercially available 4-20 mA seismic vibration transmitter in the 1980s. For the past ten years, we have continued to be an innovative leader in the reciprocating compressor monitoring equipment industry with the world’s first field configurable proximity system. We have extended that digital technology to our 5580 and SW5580 Smart Signal Conditioners, which provide the ability to extend the dynamic vibration signal while providing a 4-20 mA output to a control system. With the 5580 technology, one can look at acceleration and impact with an accelerometer on the crosshead, and rod position and rod drop with a proximity sensor near the piston cylinder packing box. Our DATAWATCH IX monitoring system builds on this configurable theme by offering a flexible monitoring module – a 4 or 8-channel system configurable for virtually any vibration or position transmitter measurement. Because our equipment can be configured for your needs, we are a one-stop shop for all reciprocating compressors in your business.
Transmitter Solution
• Simple
• Cost-effective
• Takes advantage of existing control systems, PLCs or SCADA systems
Impact Monitoring
The impact measurement was originally developed as a reliable means of protecting reciprocating compressors. Mechanical conditions such as loose bolts or rod nuts, excessive slipper clearance, worn pins, and liquid in the process are routinely detected on recips using the impact measurement. Prior to this type of monitoring, extremely skilled technicians were required if there was any hope of detecting major issues before they arose.
The IT681X Impact Transmitter outputs a current level based on the registered number of events above a user-set threshold level that occurred within a configurable time window. Metrix calls this measurement of “impact severity” – Impact. We can also provide the same impact functionality with our SA6200A accelerometer monitored on the crosshead connected to our 5580 or SW5580 Smart Signal Conditioner. Using the 5580 technology we can provide both impact and acceleration using a single sensor. An output of 4 mA indicates no impact events occurred over the threshold level within the set time window. An output of 6 mA indicates 2 impact events, 8 mA indicates 4 impact events, etc., up to 20 mA for 16 impact events. If the transmitter is set up correctly, the events should equal the number of impacts due to looseness.
Valve Temperature
Valve temperature is a proven method for detecting valve problems. Broken valves are a common mode of failure for reciprocating compressors according to industry studies. Metrix offers the ability to monitor valve temperature using DATAWATCH IX with RTD/TC input to the monitor.
Rod Drop Measurement
An indicator used to determine rider band wear is rod drop. Using a proximity probe to trend band wear helps to avoid piston-to-cylinder liner contact and associated downtime for unexpected repairs. The average position or an instantaneous position of the piston can be provided to the user with a rod drop measurement, allowing for early detection and prevention of any likely contact. The MX2034 Proximity Transmitter can be used for rod drop or rod position measurements with a 4-20 mA output to your control system, PLC or SCADA system. Using the 5580 or SW5580 Smart Signal Conditioner, with an MX2033 Proximity Driver, one can get both rod drop and rod position measurements. The SW5580 provides alert and danger relays that can be useful for early warning and shutdown.
Frame Vibration
While operational, the vibration output of machines will provide a significant amount of valuable information pertaining to the running speed and any forces acting on the machine. With an impact transmitter or an accelerometer, malfunctions associated with low-frequency and high-frequency events can be reliably detected. Metrix recommends the use of the ST5484E Velocity Transmitter for frame vibration measurements or the SA6200A accelerometer integrated to velocity using the 5580 or SW5580 Smart Signal Conditioner.
Download our Reciprocating Compressor Applications Whitepaper Download our Reciprocating Compressor Monitoring Brochure