Best Practices for Implementing Pump and Motor Condition Monitoring
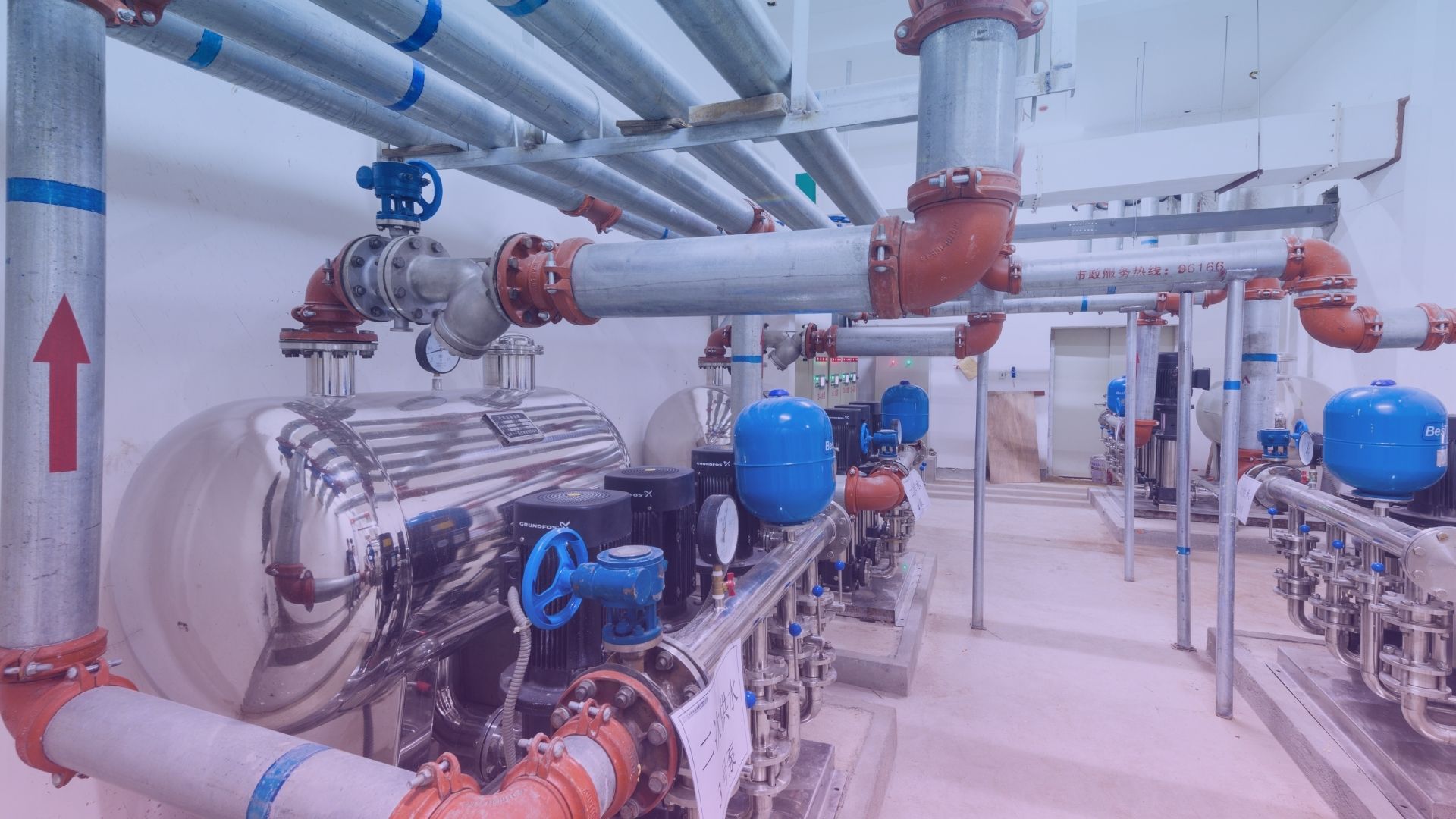
A pressure pump for running water
Pumps and motors are some of the most important machinery at the plant. They are usually integral to the process, and widely used in various industries to transfer liquids, increase pressure, or circulate fluids within systems. They play a crucial role in numerous processes, including oil and gas production, chemical processing, water supply, water and wastewater treatment, cooling systems, and many more.
Pumps move liquids from one area to another by accelerating the liquid using centrifugal forces in Centrifugal Pumps, or by grabbing a certain amount of liquid and physically pushing it towards where it needs to go using Positive Displacement Pumps, both usually driven by motors. Positive Displacement pumps are further categorized into Reciprocating and Rotary type pumps.
Maintaining pumps and motors help them last longer, and it also makes it possible to avoid process slowdowns that ultimately affect production. When you prioritize vibration monitoring for pumps and motors, you can expect to see a notable difference in your operations by observing the condition of your rotating and reciprocating assets. Monitoring for significant changes in vibration allows you to take action before you have serious machine degradation.
Pump and motor maintenance comes down to identifying and interpreting the forces that impact them. Equipment reliability depends on how the different parts of the pump and motor work together to operate successfully. If the pump experiences issues such as worn bearings, shaft misalignment, pump cavitation or other defects, it may have an impact on the motor vibration levels, and on the normal operation of the pump. Vibration monitoring sets a baseline for operators and technicians and helps them understand when a problem begins so that it can be addressed as early as possible. Instead of reacting to a mishap, they can proactively control the situation before it has the chance to develop further.
While few would argue the importance of pump and motor condition monitoring, especially considering the cost of operational shutdowns, the reality is that these machines rarely get the same attention as more critical machinery at the plant. However, despite the wide use of pumps and motors, and, oftentimes limited monitoring, these machines are by no means immune to failure. We’ll look at how to implement best practices for condition monitoring, and why it makes sense to invest in more comprehensive monitoring strategies.
Maintenance Strategies
The management of machinery is directly tied to how much value an operation gets from each machine. Vibration monitoring is a way to understand when a machine is beginning to malfunction long before it affects your bottom line.
1. Run to Failure (worst): This is the most expensive way to operate: run the machine until it fails, then replace it.
2. Preventative Maintenance (good): Repairs to the machines are made on a periodic basis, regardless of the machine’s condition. Oftentimes, the preventative repairs can be more damaging to the machine than if the machine was left alone — this is the second most expensive way to operate.
3. Predictive Maintenance (better): Repairs to the machines are made based on the condition of the machine. Using predictive technologies like vibration monitoring, thermal imaging, and lubrication analysis, operators can drastically cut back on the costs of maintenance. The key is that operators need a consistent investment in permanent vibration monitoring integrated with the existing Control System (PLCs, SCADA, RTUs, and more).
4. Proactive Maintenance (best): Repairs to the machine are made based on the condition of the machine, based on predictive technologies like vibration monitoring, thermal imaging, and lubrication analysis. These tools combine continuous vibration monitoring with data correlation with the plant process parameters of pressure, flow, power level, capacity, etc. This is the most inexpensive way to operate, but it has the highest initial startup cost.
The point of vibration monitoring benefits is to give operators as much insight as possible into their machines. Mechanical failures rarely occur in a vacuum. There are typically dozens of signs before a plant should shut down a machine, but these signs aren’t always noticeable if you don’t have the right vibration monitoring equipment. That’s why it pays to invest in predictive and proactive maintenance programs.
Data Collection Methods
The best way to monitor a machine is to have XY vibration sensors at each bearing, thrust monitoring, and a phase trigger, however this amount of monitoring is often not practical given the potential return on investment the monitoring system would provide if it could save one day of downtime within a three-year period. Let’s use a power plant as an example.
150 Megawatt Combined Cycle Gas Fired Power Plant Example
In order for the power plant to operate, the equipment must be in good condition. For example, the Gas Turbine, the Steam Turbine, their associated generators, the Feed Pump, the condensate pumps, the cooling system, etc. all must be in working order before operations can commence.
The margin on 1 megawatt-hour (MW-hr) of electricity is a minimum $45 USD / MW-hr, sold to wholesale customers (this is a $0.045 USD per kW-hr rate). So, one hour of unscheduled downtime equates to a Lost Opportunity Cost of $6750 (150 MW-hrs/hour x 1 hour x $45/MW-hr = $6750). One day of unscheduled downtime results in a Lost Opportunity Cost of $162,000 per day ($6760/hour x 24 hours = $162,000). Customer Value = Repair Cost + Unscheduled Downtime = + $162,000 minimum per day.
Note: Components within the combined cycle plant may be redundant or, if unavailable, may reduce plant capacity. This applies to the condensate pumps, cooling water pumps, cooling tower fans, etc., meaning they have less of a financial impact on the plant. For example, let’s assume that if a circulating water pump is out of commission, the plant capacity is reduced by 20%. That would mean that the Customer Value is 20% of the values calculated above or $32,400 per day ($162,000/day x 20% = $32,400).
In this case, the circulating water pump may not justify a full vibration monitoring system but can easily afford XY Velocity Transmitters at each bearing, transmitter thrust monitoring, as well as speed monitoring, with all the output signals going to the control system.
In other words, the Gas Turbine, the Steam Turbine, their associated generators, and the Feed Pump may easily justify a full Metrix Transducer Suite of Sensors (e.g. XY Bearing Vibration, Thrust Monitoring, and a once-per-turn Phase Marker, along with a machinery protection system), with full integration to the Plant Information Network, given that the savings for just avoiding one day of downtime within a three year period of time justifies the expense. Whereas the condensate pumps, circulating water pumps and cooling tower fans would justify a lesser system utilizing the control system as the shutdown system, given the same criteria of saving one day of downtime within a three-year period. Metrix often sees customers using one or two Metrix vibration transmitters or the Metrix 5580 / SW5580, or DATAWATCH IX Solution, integrated to the appropriate Control System and Plant Information Network due to the return-on-investment calculation.
Sensor solutions are so versatile now that power plants can easily use them in even the most out-of-the-way areas. This allows engineers and technicians to get the flexibility they need without having to put themselves in harm’s way to get the job done.
Machinery Health Monitoring
Monitoring system implementation for pumps and motors may be straightforward, but it requires expertise to set up the system and ensure proper monitoring. We have found that using statistical averages are effective when setting alert and shutdown values. Over time, when a machine is under constant load and speed, we have found that the vibration level variation follows a normal distribution. In other words, the vibration variation is evenly distributed on each side of the average value. Since the vibration usually provides a normal distribution, the average value and the standard deviation now have meaning. One can use the standard deviation to set the alert and danger levels using standard control theory. The alarm levels can be set by using two standard deviations from the mean for the alert alarms, both over and under alarms, and using three standard deviations from the mean for the danger alarms. Three standard deviations from the mean, or average, means that the vibration level has changed significantly enough to warrant investigation.
Pumps and motors have a few unique challenges when it comes to accurate data collection. For example, the pump valve lineup will have an impact on pump performance due to the flow through the machine. If the suction valve is shut, the machine will experience a loss of flow, which could actually cause the vibration level to go down, due to a lack of force on the impeller blades (no cut water action between the blades and the narrow space at the diffuser outlet). The no flow condition through the machine will result in a lack of cooling, which could result in pump failure. The under alert alarm, mentioned above, should be able to alert you of this bad valve lineup situation. Another case is, when a pump loses Net Positive Suction Head (NPSH) the vibration levels are expected to go up, due to the cavitation that results when the vapor bubbles collapse. The cavitation results in broadband noise, which can excite numerous resonant frequencies found within the pump and its associated structure.
Tips and Takeaways for Machine Maintenance Optimization
You can’t get away from proper installation, lubrication, alignment, balancing, and monitoring of your pumps and motors. Trying to shortcut any of these best practices, will result in premature failure of your pumps and motors. If a pump and motor are a key part of your process flow (or even if it interacts with key components of your process flow), investing in a vibration monitoring system saves you money over time.
Consider the cost of a single breakdown, not just in terms of direct repair or replacement costs, but also the lost production that you’re not able to get back. That savings of one day of downtime equates to money. At Metrix, we believe if we can save you one day of downtime within a three-year period, that justifies the cost of the vibration monitoring system employed. Return on investment is a key calculation to determine the amount of monitoring you should employee on a pump and motor combination.
If you have any questions on return-on-investment calculations, please contact a Metrix representative and we’ll be happy to take a look at your process and determine the savings based on avoiding unplanned downtime.