How Digital Proximity Systems Improve Reliability of Rotating and Reciprocating Machinery
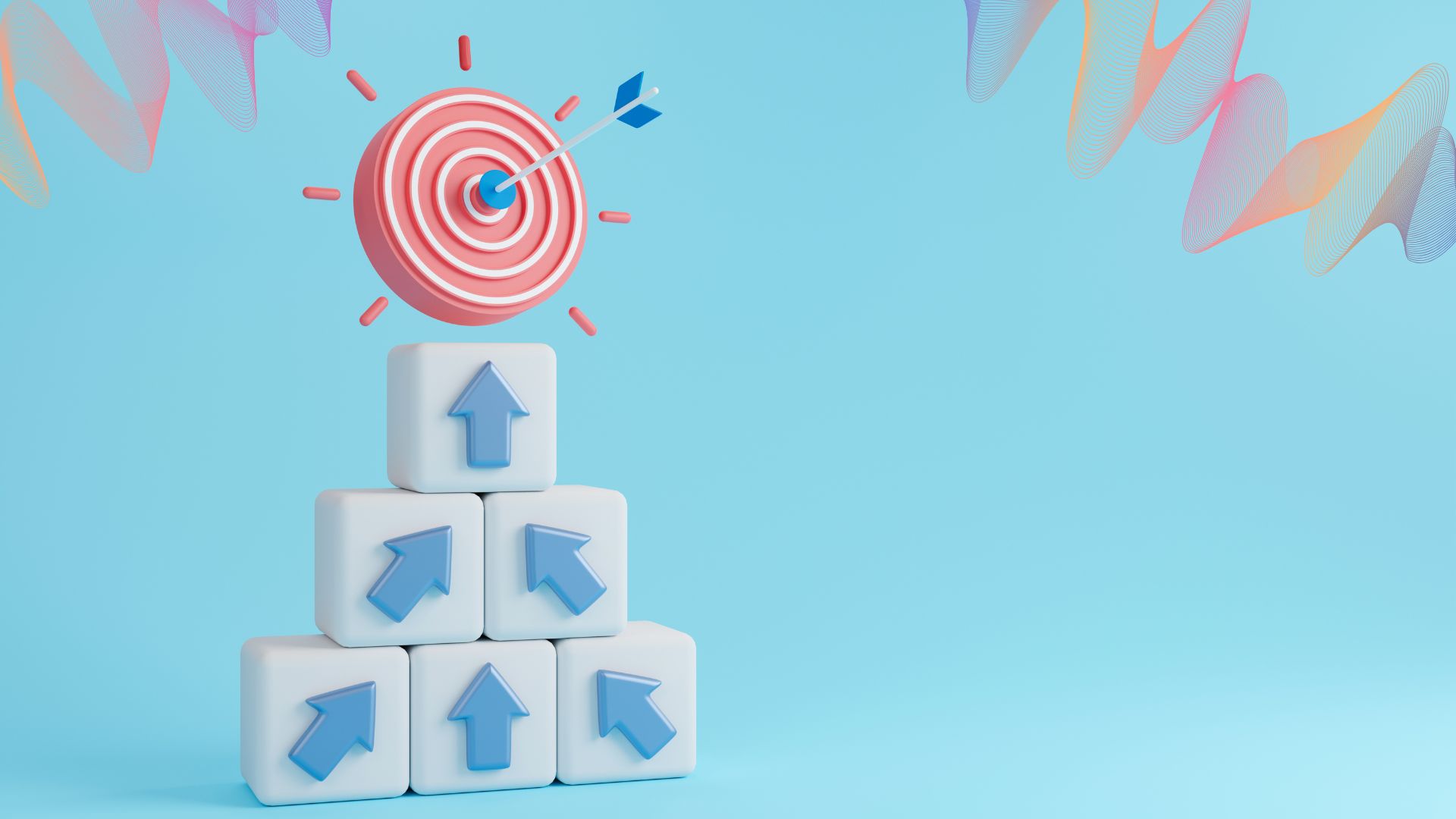
Improving reliability of rotating and reciprocating machinery
Proximity systems are used to monitor the vibration, position and speed of fluid film bearing machines. They are also used to measure rider band wear on reciprocating compressors and as a source of phase measurement for machinery diagnostic or condition monitoring systems.
Due to the damping in fluid film bearing machines, it is often the case that the vibration of the rotor does not make its way to the casing. Proximity probes watching the movement of the shaft in both radial and axial directions provide the necessary information to make sound machinery condition decisions. In some cases, like gas turbines, casing sensors are used to supplement the shaft observing proximity probes. The digital proximity system allows one to ensure that the vibration and position signals they’re seeing are accurate. The features of the Digital Proximity System (DPS) like crosstalk elimination, TIGHTVIEW®, and extended range, are but a few of the features that improve the accuracy of the proximity system. In speed and phase measurements, the digital proximity system can enhance the pulse going to a monitoring system, improving the accuracy of the measurement.
In reciprocating machines, the rod drop measurement is suspect because the average scale factor is used instead of the actual scale factor of the proximity system looking at the piston rod. For rod drop or rod position, proximity sensors are usually located near the cylinder packing to measure piston rod movement and predict rider band wear. The digital proximity system is used to obtain API 670 accuracy using the actual piston rod material, this is in lieu of using an average scale factor that does not necessarily reflect the characteristics of the piston rod. Oftentimes a customer will settle on an average scale factor for the proximity system because they can’t calibrate to the shaft material. The digital proximity system eliminates the average scale factor problem, allowing for the rod drop or rod position measurement to reflect the actual condition of the machine.
How Do Digital Proximity Systems Work?
Digital Proximity Systems (DPS) are like Analog Proximity Systems only better. They provide the standard 7.87 mV/µm (200 mV/mil) or 3.93 mV/µm (100 mV/mil) sensor output. The major difference between the two systems is that the Digital Proximity System can be configured in the field for probe type, system length, and target material.
The DPS uses 1.1 MHz oscillator demodulator frequency for the radio frequency signal that is used to create the eddy currents in the target material. The DPS can modify this frequency depending on how it’s configured. The probe type system length and material type will impact the oscillator demodulator frequency. Since we can control the oscillator demodulator frequency, it gives Metrix the ability to do special things like Crosstalk Elimination, TIGHTVIEW®, Pulse Height Adjustment, and many others.
Because the DPS can be calibrated in the field with an unknown material type, customers don’t have to settle for using an average scale factor. They can use the calibrated Incremental Scale Factor (ISF) to obtain a more accurate vibration amplitude, position and phase reading.
How Do Different Industries Use Digital Proximity Sensors?
Proximity systems are used in every industry that employs rotating machinery using fluid film bearings, and on reciprocating machines to monitor rider band wear and possible malfunctions. The DPS is used wherever you’re using proximity systems to monitor machinery. We’ll look at some of the most common applications of people using the DPS and why:
● Spare Parts: The DPS can be configured to work with almost any legacy proximity system, not just Metrix, but other manufacturers as well. Customers often use the Metrix DPS during outages, overhauls, and retrofits because of its versatility in the field. Customers can be assured they can get their proximity systems to work without having to worry about having the exact oscillator demodulator for their particular situation.
● Lead Times: Metrix builds tens of thousands of proximity systems. Customers depend on us to be able to provide them proximity sensors in a timely fashion. Metrix can do this because they use a single platform and can configure it to the needs of the customer. The single platform allows Metrix to minimize the number of parts to create the DPS, and not to have to worry about additional parts for a customer’s particular service.
● Reciprocating Machines: Customers often complain about their Rod Drop measurements. Metrix eliminates these complaints by providing a system that is accurate for the application. Metrix provides linearity for the material used to create the piston rod and prevents the customer from using the Average Scale Factor (ASF), which is a major source of air in these measurements.
Whether it’s power generation, refining, mining, manufacturing, paper production, or water and wastewater, the DPS provides the accuracy, reliability and versatility required of the 21st century.
Digital Proximity Systems by Metrix
At Metrix, every product in our catalog is a result of expert engineering. We listen to our customer’s concerns, so engineers, managers, and technicians can trust the data they're seeing no matter how they've configured the DPS. If you have any questions about the Digital Proximity System, please contact us.
Metrix - One Digital Proximity System - Is All You Need