The Advantages of Proximity Vibration Monitoring for Critical Machinery
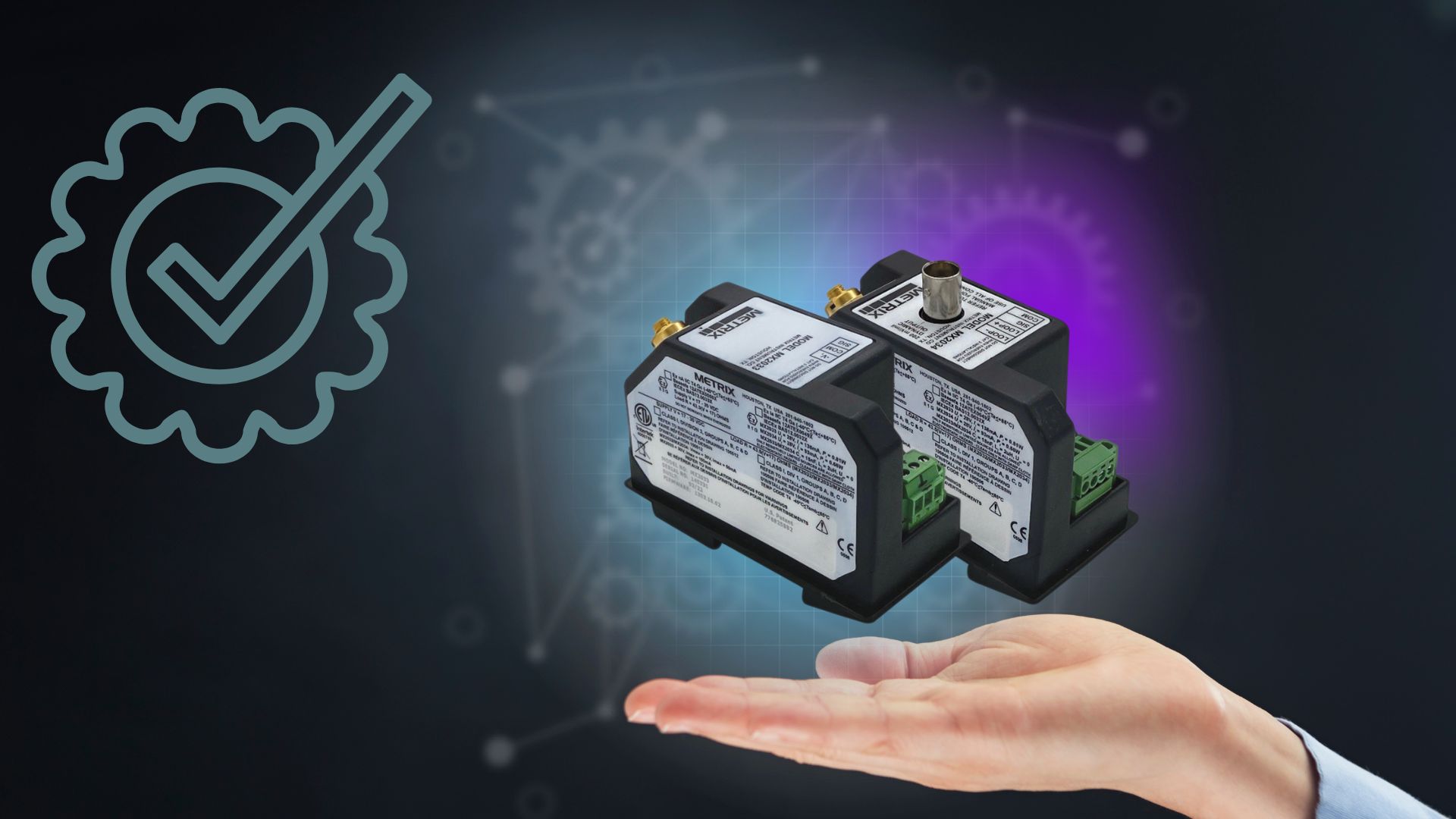
The MX2033 Driver and MX2034 Transmitter are premier proximity vibration monitoring devices from Metrix
It has long been accepted that monitoring fluid film bearing machines with proximity sensors is a best practice. There are some exceptions, like reciprocating compressor crankshaft monitoring, but very few. The fluid lubrication in a fluid film bearing usually provides significant damping to the rotor vibration, such that the vibration is not sensed on the casing. The fluid wedge that is formed by the rotor rotating in the bearing clearance provides a shock absorbing effect and allows relative motion between the rotor and casing, which makes using proximity sensors a perfect application. In some cases, if one allows the vibration amplitude to become high enough to allow the rotor to come in contact with the casing, then a casing sensor may pick up the vibration signal. The problem with using the casing sensor as your primary means of monitoring the fluid film bearing machine, is the lack of information from the sensor to indicate an issue or problem. Measuring casing vibration with a fluid film bearing usually does not provide enough information to prevent machine damage.
In industrial gas turbines, the rotor is heavy when compared to the casing mass, and this results in more casing movement as compared to typical industrial machinery. With industrial gas turbines, proximity sensors monitoring the rotor and casing sensors monitoring the casing are needed for adequate vibration protection and monitoring. This can also be true of large steam turbines, usually greater than 100 megawatts.
The reason why we don’t use proximity sensors to monitor a reciprocating compressor crankshaft, which is supported by fluid film bearings, is because of the bearing support structure. The numerous bearings in a relatively short span, makes the system very stiff, which doesn’t allow for much relative movement between the crankshaft and the casing. Since there isn’t a lot of relative movement between the crankshaft and the casing, it makes the use of proximity sensors, to monitor crankshaft vibration, impractical.
Proximity probes measuring vibration, position, speed and phase on fluid film bearing machines have been effective at protecting critical assets for the past 60 years. The ability to look inside the machine without taking it apart has been invaluable to the oil & gas, power generation, and other process related industries. The data from a proximity system provides the necessary picture to make effective diagnostic recommendations.
Why Proximity Monitoring Works
For critical machines, the vibration monitoring solution should depend upon the cost of Unscheduled Downtime. Unscheduled Downtime caused by a problem coming from a critical rotating or reciprocating machine is the costliest downtime for a plant. The plant loses money from lost profits (Lost Opportunity Cost = loss of profitable output), expedited repair, material and labor costs, standby labor costs, quality issues, customer trust / delivery issues, and most importantly personnel safety concerns. The sensory solution employed on a machinery asset depends upon the probability of an unscheduled downtime event. If the asset downtime does not present a risk to personnel, the facility or community, then the vibration monitoring solution is minimal.
Proximity sensors can be used directly to a monitoring system or, if using a proximity transmitter, directly to a control system. When used with a monitoring system, they are an excellent source of discrete vibration parameters like overall vibration, gap voltage, 1X amplitude and phase, 2X amplitude and phase, nX amplitude and phase, and Not 1X. Each of these discrete parameters are useful for determining specific malfunctions. However, oftentimes, the time and effort to set these parameters up, and maintain them in the monitoring system, to make them meaningful, is not justified. In most cases these parameters are present in the Vibration Monitoring System (VMS) but are not used. Usually only the direct amplitude is used, and it is fed to the Control System, like a vibration transmitter output. Typically, the direct amplitude from a rack-based system is used for a vibration shutdown signal. Getting the discrete vibration parameters into the Control System is not justified, unless the discrete parameters are maintained. Since, in most cases, they are not maintained, the expense for the VMS as an addition to the Control System is not justified unless the scan rate of the control system is more than 0.1 seconds. Long scan periods over 0.1 seconds make the use of a Control System as a protection system not very effective. To use the Control System as a protection system, the scan rate must be less than 0.1 seconds.
When industrial sites vary in scope, size, and operations, proximity monitoring gives operators and engineers a way to understand even the most remote fluid film bearing machines. Proximity sensors can be used to accurately capture the level of vibration.
Early Warning Signs
It’s not easy to predict the future, no matter how detail-oriented a professional is. New equipment may be introduced at any moment, with leaders demanding seamless integration into the rest of the operation. What these decision-makers may not understand is that vibration is a ratio of forces to stiffnesses, and the forces and stiffnesses change as the operating conditions of the machine change, making measuring vibration challenging at industrial sites. The earliest warning signs may be misdiagnosed or dismissed entirely.
With proximity sensors, it’s easier to foresee potential equipment failures. Proximity sensors provide a picture of the operating condition of the most critical machinery on site, alerting the staff to the beginning of the vibration changes before the changes in forces or stiffnesses have the opportunity to damage the machine in question or the equipment that surrounds it. This isn’t just important to avoid major damage, the data fed back to the staff helps them improve their maintenance schedules, allowing for the repairs and tweaks to critical machinery long before it has a chance to spiral out of control.
Real-World Examples
Machinery that substantially affects your business revenue is critical. Having the right monitoring system on those critical machines is essential to maintain production. Industry professionals use proximity sensors to detect changes in vibration, position, and/or speed to alert them to machinery problems.
150 Megawatt Combined Cycle Gas Fired Power Plant Example
In order for this power plant to operate, the critical equipment must be in good condition. For example, the Gas Turbine, the Steam Turbine, their associated generators, the Feed Pump, the condensate pumps, the cooling system, etc. all have to be in working order before operations can commence. The gas turbine, the steam turbine, the associated generators, and the feed pumps usually have fluid film bearings due to the size and speed of the machines. These fluid film bearing machines are usually monitored with a full suite of proximity probes. XY probes at each bearing, Thrust probes and a Phase Trigger, among other sensors. The justification for these sensors is easily found from a quick Return on Investment (ROI) calculation. For example:
The margin on 1 megawatt-hour (MW-hr) of electricity is a minimum $45 USD / MW-hr, sold to wholesale customers (this is a $0.045 USD per kW-hr rate). So, one hour of unscheduled downtime equates to a Lost Opportunity Cost of $6750 (150 MW-hrs/hour x 1 hour x $45/MW-hr = $6750). One day of unscheduled downtime results in a Lost Opportunity Cost of $162,000 per day ($6760/hour x 24 hours = $162,000) Customer Value = Repair Cost + Unscheduled Downtime = + $162,000 minimum per day.
In other words, the Gas Turbine, the Steam Turbine, their associated generators, and the Feed Pump easily justify a Full Metrix Transducer Suite of Proximity Sensors (XY Bearing Vibration, Thrust, Speed, and/or Impact) with full integration to the Plant Information System.
Sensor solutions are so versatile now that power plants can easily use them in even the most out-of-the-way areas. This allows technicians to get the flexibility they need without having to put themselves in harm’s way to get the job done.
Metrix has worked with countless companies that have come to rely on both our expertise and product catalog. One notable example was a methanol producer that had a critical machine train unexpectedly go down. By working closely with the client, we were able to develop a vibration monitoring solution that would identify failure modes. Once it was implemented, the staff was able to accurately detect compressor valve failure, an event that could have ultimately cost the company around $100,000 per day.
Critical machinery is a high-ticket investment for a company. To improve the lifespan and ROI of any machine, it needs to be properly configured, monitored and maintained. Proximity monitoring systems from Metrix are designed to give operators enough time to intervene long before there's damage to the equipment, its surroundings, or the production schedule.
If you have any questions on return-on-investment calculations, please contact a Metrix representative and we’ll be happy to take a look at your process and determine the savings based on avoiding unplanned downtime.