Selecting a Signal Conditioner
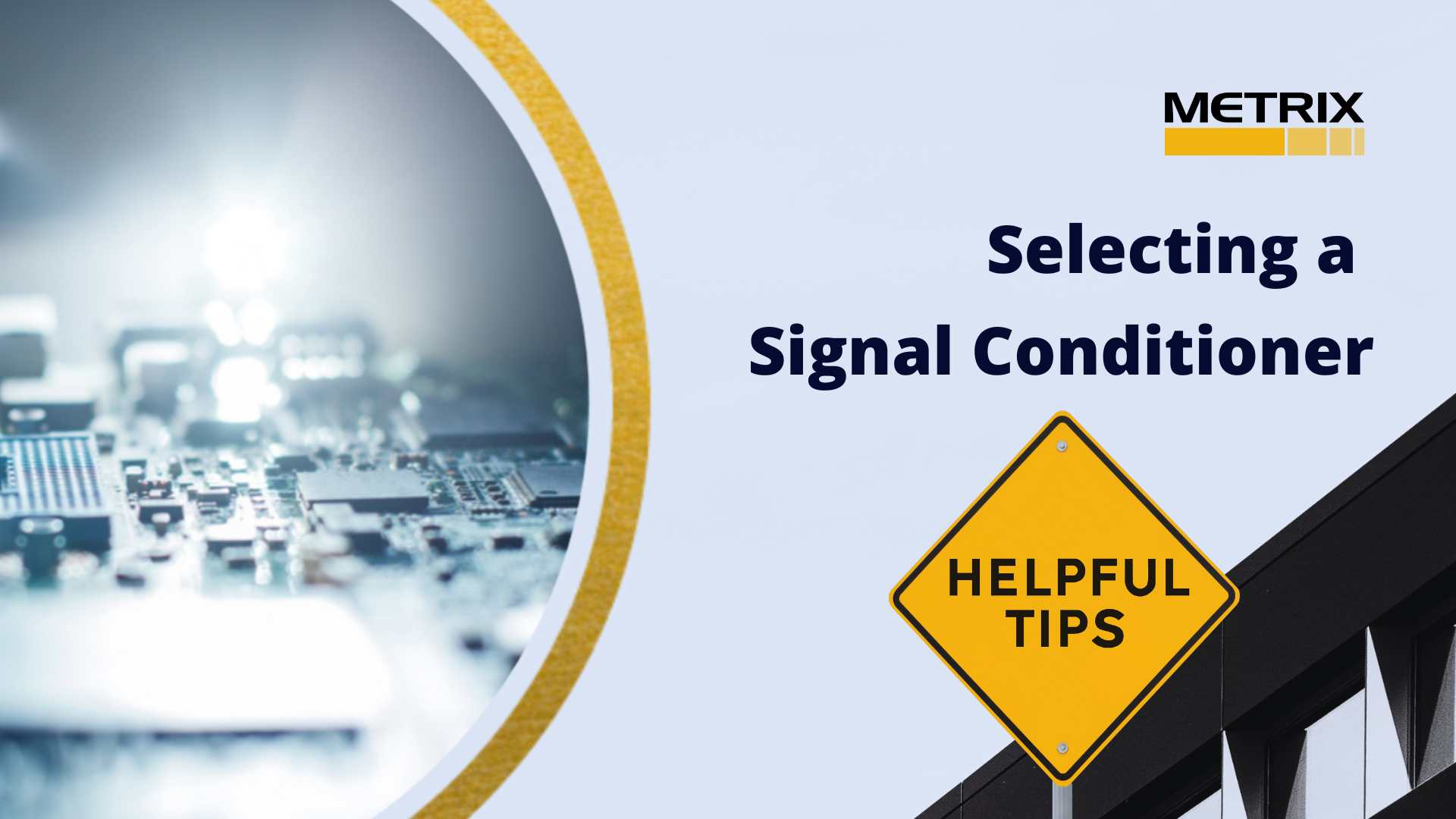
By understanding the different types of signal conditioners, you can choose the right one for your needs.
Common Types of Signal Conditioners
Signal conditioning is used in your radio, in your surround sound and in your television. This blog post will discuss the signal conditioning as related to vibration sensors. The signal conditioners we will be discussing will be able to take a displacement, velocity or acceleration vibration signal and convert it into a 4-20 mA output and/or boost the incoming dynamic signal so it can be sensed by a vibration monitoring system.
In vibration monitoring, signal conditioners are used to ensure vibration readings are accurate and reliable, especially over long distances. Without signal conditioners, you wouldn't be able to trust the readings you're getting from your various machines if the monitoring system is greater than 300 meters away from the sensor.
What Is a Signal Conditioner?
A signal conditioner takes a raw dynamic signal and converts it into a proportional 4-20 mA output. What that means is that if you have a signal that is between 0 and 1 ips peak, you can scale the signal conditioner so zero vibration equals 4 mA and one inch per second would equal 20 mA. At the same time the signal conditioner boosts the raw dynamic signal using a unity gain amplifier so that there is no degradation of the dynamic signal to the vibration monitoring system (VMS). The raw dynamic signal from a proximity sensor, velocity sensor or accelerometer is usually limited to 300 meters due to high frequency (> 1000 Hz) attenuation. The signal conditioner prevents this degradation and provides the raw dynamic output to the VMS up to 300 meters away.
There are many different types of signal conditioning, but the five most common include filtering, amplification, isolation, excitation, and linearization. Metrix provides signal conditioners that can do all five.
Signal Conditioner #1 - Filtering
The first type of signal conditioner is filtering a raw dynamic signal. In the filtering process, unwanted vibration frequencies are removed from the signal being monitored. This ensures that only important information is being sent to the machine operator. There are three main types of filters: low-pass, high-pass and band pass. Low-pass filters do exactly as they state, they remove vibration frequencies above a particular frequency, while passing the frequencies below the filter. High-pass filters remove vibration frequencies below a certain frequency, while passing the higher frequencies above the filter. A band pass filter takes advantage of both the high and low pass filters as described above and passes the band in between these two frequencies. This ability to filter is important in vibration monitoring as you often want to separate the rotor related frequencies (1/4X to 3X) from the bearing related frequencies (1 to 6 times the outer race ball pass frequency).
Signal Conditioner #2 - Amplification
The second type of signal conditioning is known as an amplification. This is easily noticed when you are using your car radio or surround sound system – you just turn up the volume via the dial or your remote control.
In vibration signal conditioning, this amplification is done with a unity gain amplifier so that we do not distort the signal that is coming from the machine. It’s important we maintain the integrity of the amplitude of the signal because it relates to the severity of the vibration.
Signal Conditioner #3 - Isolation
A third type of signal conditioning is using an isolation conditioner. It is used in hazardous areas to separate the sensor in the hazardous area from the monitoring equipment that is usually in a safe area.
In vibration monitoring, this type of signal conditioner is called a barrier. This is used to protect the process and the monitoring equipment from damage caused by unwanted electric transients. Isolation can be achieved in a number of ways, but the most common method uses a transformer. This separates the signal so that a short on the sensor side does not cause a spark and potentially a fire or explosion in hazardous areas. This protects equipment and people from any damage from an unwanted electrical fault.
Signal Conditioner #4 - Excitation
The fourth type of signal conditioning is known as excitation signal conditioning. In vibration monitoring, this is often used in piezoelectric accelerometers. As the piezoelectric crystal is stressed by the movement of the sensor, it generates an oscillating electric signal that can be amplified and detected. The stressing of the crystal is what causes the excitation that can eventually be measured. The excitation is proportional to the amount of the vibration and is usually 100 mV/g.
Signal Conditioner #5 - Linearization
The fifth and final type of signal conditioner is a linearization conditioner. This conditioner is used typically in proximity systems to straighten out the non-linear curve that is generated by an eddy current proximity system. A radio frequency signal is emanated from the probe tip and creates eddy currents in the surface of the material. These eddy currents cause losses in the signal that can be linearized and be made proportional to the gap between the probe tip and the surface material. The Digital Proximity System (DPS) can take advantage of different probe types, different surface materials and system lengths to create a linear response.
These are the five most common types of signal conditioners. By understanding all of them, you will know when they are appropriate to use with your rotating and reciprocating machinery.
Tips for Choosing a Signal Conditioner
Now that you know the five most common types of signal conditioners, here are a few tips to help you choose the right one for your needs:
- Know the purpose of the signal conditioner. What are you trying to achieve?
- Consider the environment in which the signal conditioner will be used. Will it be exposed to a hazardous area?
- Consider the bandwidth of the signal. What is the frequency range of the vibration you are trying to measure?
- Choose a signal conditioner that's easy to use and can be configured onsite. The last thing you want is to spend hours trying to determine how to use it.
When it comes to monitoring vibration, signal conditioners are an important tool. By understanding the different types and how they work, you can choose the right one for your needs. With these tips, you'll be on your way to keeping your machinery running smoothly. If you have any questions regarding signal conditioners or how to choose the right one for your needs, contact the experts at Metrix Vibration.