The Fundamentals of Signal Conditioning and Vibration Monitoring
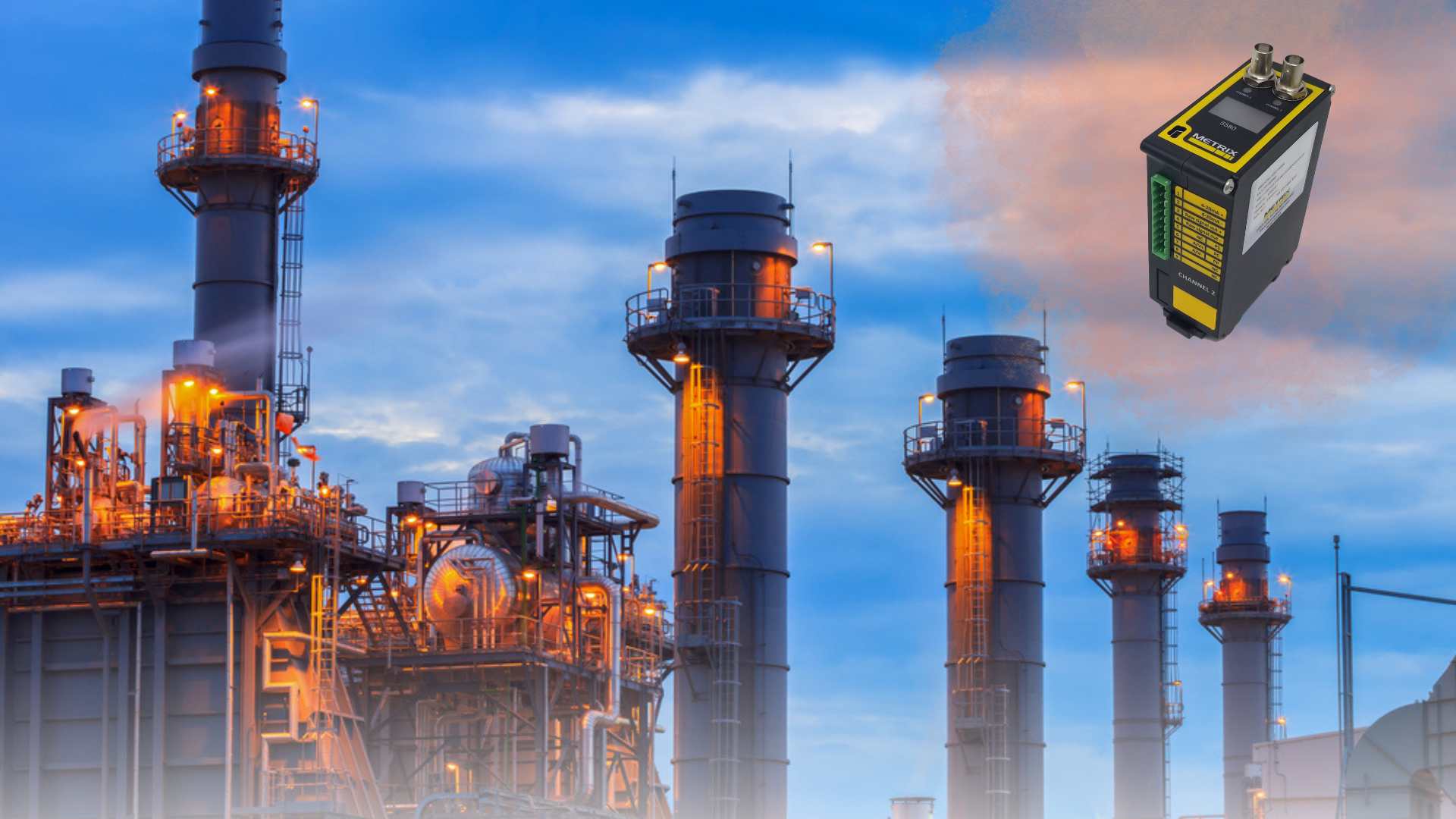
Signal conditioning and vibration monitoring is necessary for machine maintenance
There is a fundamental need for remote vibration monitoring. In today’s plant, people want to know and control parameters such as flow, temperature, pressure, liquid level, etc. of industrial processes to produce quality products. There are various rotating and reciprocating machines in large industrial process plants, where variables such as shaft vibration amplitudes, casing seismic vibrations, bearing temperatures, lube oil temperatures and seal oil pressures are in need of measurement. These parameters are critical for smooth running machines and to prevent the catastrophic failure.
Signal conditioning is a powerful tool you can rely on to measure, control and monitor parameters that you are interested in, as well as reduce the number of erroneous readings. We’ll look at how vibration monitoring works in a plant and why it’s so important to have flexible products.
What Is Signal Conditioning?
Why is signal conditioning in refining, chemical plants, power generation, wastewater treatment facilities, and other industrial processes necessary? Signal conditioners can improve accuracy and reduce risks within a facility. Signal conditioning is the process of converting a sensor signal into information that can be used within a protection system, by a control system, and into other digital formats. Signal conditioning converts and amplifies an input signal (electrical or mechanical signal) into an output signal. For instance, if a standard accelerometer signal is a low voltage, you can amplify it for remote monitoring. The form of an output signal after conversion is easily identifiable and compatible with data acquisition or control systems.
A digital signal conditioner is able to be configured for different functions and is compatible with different types of vibration transducers, which can provide accurate measurements.
Signal conditioning circuits can allow all of your machinery to run more smoothly, particularly when you find conditioners that are as versatile as your system needs them to be. You can purchase signal conditioners with different channel options and scale outputs that can be applied to anything from engines to pumps, to turbines.
Signal Conditioning Examples
It’s worth noting that there is no one-size solution for signal conditioning. Conditioning depends upon the machine type and the vibration suite used to monitor the machine. Conditioning is specific to the sensor in question, and it all starts with understanding your channel mix. For instance, on a large compressor, you should monitor shaft vibrations, thrust position, speed, phase angle, and bearing temperatures as a minimum. In some application scenarios, casing vibrations and other parameters are in need of measurement as well. These measurements come from several types of sensors or transducers, like a proximity sensor, to monitor vibration, thrust position and phase angle, as well as casing mounted transducers like accelerometers or velocity sensors to measure casing movement and thermocouples to measure bearing temperature. These sensors, or transducers, combine signal conditioners as a system accessing signals and processing data to provide you information on the condition of the machine. In other words, this is less about the individual sensor and more about how these sensors, along with signal conditioners, interact with your data acquisition or machine-control system. We’ll look at what this means when you’re trying to condition multiple sensors for complex operations.
Adjust Signal Voltage
The ideal analog-to-digital converter (ADC) range will depend on the sensor in question. Getting your signal into the correct range may involve either increasing (amplifying) or decreasing (attenuating) the voltage levels. When you increase the voltage levels of your signals, you improve the measurement resolution of your signals and increase their sensitivity. In Metrix equipment, this is done by changing the scale factor to what you actually need to measure the vibration. For a vibration signal of 5 mm/s (0.2 ips), it would be more accurate to have a scale range from 0 to 25 mm/s (1.0 ips) than to have one from 0 to 100 mm/s (4.0 ips). The resolution is better at the smaller scale range.
Filter Noise
Noise can become a major disruptor for sensors and signals, but not all noise threatens your operations. Signal conditioning can help you reject unwelcome frequencies by filtering everything that fits within a pre-configured filter range. The exact range will depend on the signal in question.
The most common way to filter your signals is through low-pass or high-pass filtering. The former will limit the bandwidth to help certain channel openings become more identifiable (as they can otherwise be clouded by noise). The latter will pass signals that surpass a specific frequency and suppress signals that fall below a certain frequency. You’ll see low-pass filters used most often in sound and vibration applications. In Metrix equipment, we often use bandpass filtering to aid the user in setting up low and high pass filters.
Isolation of Dangerous Voltages
If a voltage reaches too high a peak, it can harm the entire system. The more you can separate these high DC voltages from the major components of your operations, the more protected the system will be. Isolators can also potentially filter unwanted noise, which may eliminate the need for additional low-pass or high-pass filters.
Excitation
If you need an external voltage for the sensor, this is called sensor excitation, also knowns as active sensors. The accuracy and stability of these devices will rely heavily on the precision of the external source.
Vibration Monitoring and Metrix
Metrix is known for helping clients reduce the potential of machine failure by offering affordable machinery protection. While our products are relatively simple in that they don't overcomplicate an employee's or manager's jobs, they're designed to be flexible enough to work within different monitoring and control systems.
We have designed a number of signal conditioners and accessories that can help you set your vibration limits and properly monitor your machinery. Our signal conditioners convert voltage signals from an accelerometer, velocity sensor or proximity probe into a 4-20 signal that can be conveyed to a Control System, Programmable Logic Controller (PLC), or Supervisory Control and Data Acquisition (SCADA) System up to 2 kilometers away. Using a unity gain amplifier, we also boost the incoming raw signal so it can be conveyed an additional 300 meters (1,000 feet) without signal degradation. Read on to learn more about our Signal Conditioners including the 5580 Smart Vibration Signal Conditioner or contact technical support in case of any questions. We look forward to hearing from you.